Система рекуперації теплової енергії від гвинтових компресорів під час виробництва ПВХ профілів
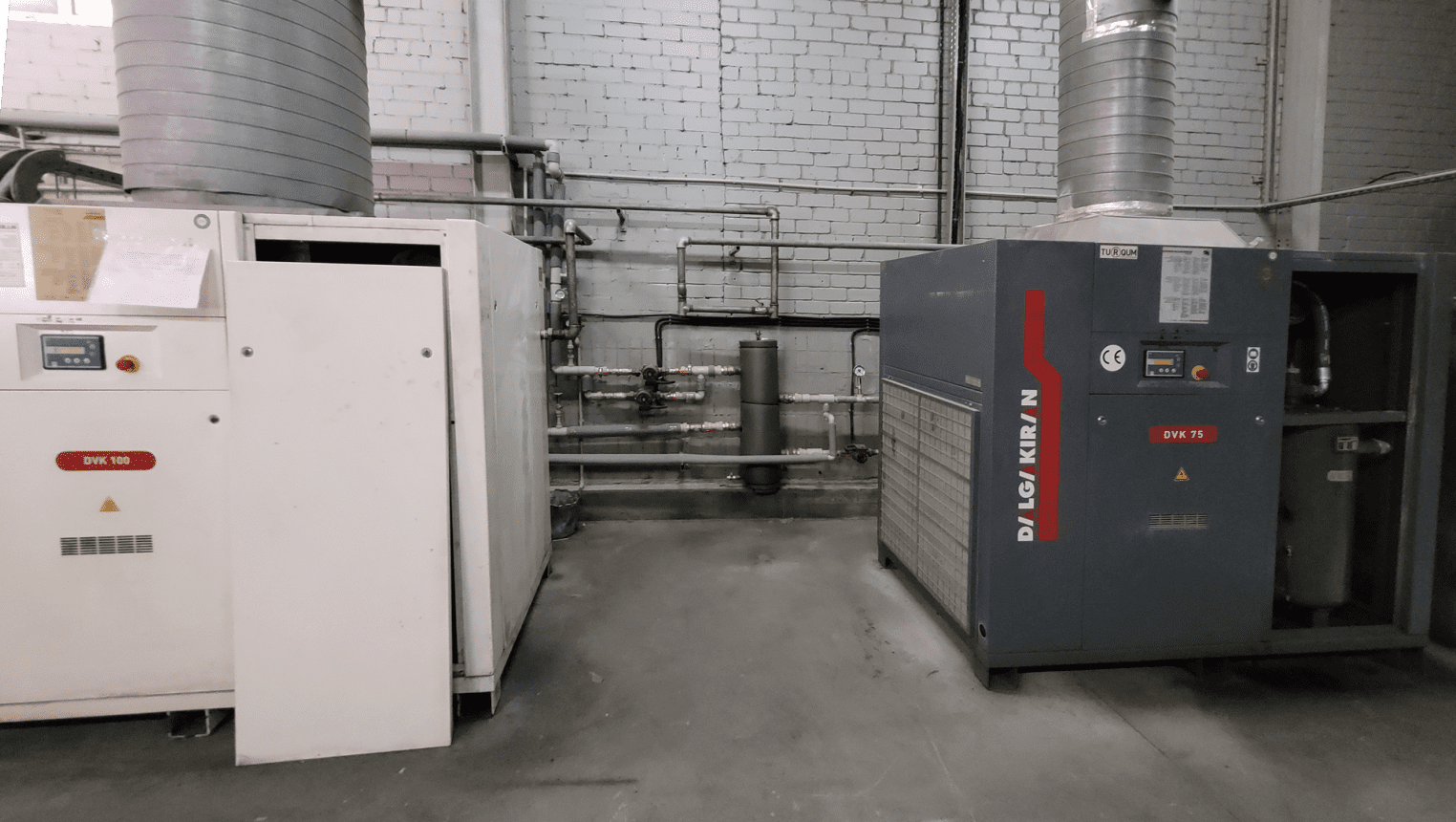
Для більшості підприємств одним із основних показників, що впливають на собівартість виробляємої продукції, є вартість енергоносіїв, які використовуються на виробництві. Як і у всьому світі, на українському енергоринку спостерігається тенденція сталого зростання цін на енергоносії, тому компанія “Далгакиран компресор Україна” активно пропонує своїм клієнтам та партнерам комплексні рішення з використанням енергозберігаючих технологій «під ключ». Одним із таких партнерів є компанія “Міропласт”.
“Міропласт” – лідер ринку ПВХ-профілю в Україні. Компанія постійно нарощує свої виробничі потужності та розширює асортимент. Вироблені профільні системи ПВХ дозволяють створювати функціональні та естетичні вікна і двері для дому, офісу, комерційних та виробничих приміщень, забезпечуючи безпеку і відмінну звуко- та теплоізоляцію.
Одним з основних енергоносіїв, що застосовуються у технологічному процесі виробництва профілів “Міропласт”, є стиснене повітря, яке виробляється гвинтовими компресорами. Для забезпечення максимальної енергоефективності використовуваних компресорів DALGAKIRAN наші фахівці запропонували впровадити систему рекуперації теплової енергії, що виділяється обладнанням у процесі стиснення повітря, і направити її споживачеві замість скидання у навколишнє середовище, як це було організовано раніше.
Восени 2021 року фахівці “Далгакиран компресор Україна” підготували та направили Замовнику техніко-комерційну пропозицію з описом технічного рішення, що включає економічне обґрунтування впровадження цього проекту. Після спільної оцінки ризиків зі спеціалістами “Міропласт” було ухвалено рішення про організацію системи рекуперації теплової енергії з компресорного обладнання, розташованого на території ділянки “Водопідготовки №2”, а саме – гвинтових компресорів DALGAKIRAN DVK-100 та DVK-75.
Технічне рішення
Згідно з проектом, споживачем теплової енергії є цех ламінації, технологічний процес якого вимагає підтримки температурного режиму в приміщенні не нижче 22 °C у будь-який період року. Раніше цей температурний режим дотримувався за допомогою газових руфтопів. Споживання природного газу у зимовий період у середньому становило 800 м3/добу.
Заявлена теплова потужність, яка отримується при використанні запропонованої системи рекуперації теплової енергії, становить не менше 110 кВт.
Запропонована система рекуперації теплової енергії складається з двох гідравлічних контурів:
- первинний контур (контур рекуперації), що складається з високоефективних рекупераційних теплообмінників та насосних агрегатів, необхідної продуктивності для кожного з компресорів;
- вторинний контур (контур системи опалення цеху ламінації), що складається з магістральних трубопроводів, циркуляційних насосів та опалювальних приладів у вигляді фанкойлів у кількості 6 шт. Управління фанкойлами здійснюється за допомогою контролерів із вбудованими датчиками температури в цеховому приміщенні, з попарним підключенням обігрівачів, що забезпечує ефективне та незалежне керування тепловими потоками (один контролер керує двома фанкойлами).
Взаємодія даних контурів з різними витратно-напірними характеристиками організована за допомогою гідравлічного змішувача, який стабілізує системи та ефективно розподіляє гідравлічні потоки. Як теплоносій використовується вода.
В результаті реалізації цього проекту у грудні 2021 року Замовник отримав 111,65 кВт/год надлишкової теплової енергії, яка раніше скидалася в атмосферу, з наступним розподілом температур теплоносія:
- первинний контур (контур системи опалення цеху ламінації):
Т подачі = 73 °С; Т звороту = 57 °С;
- вторинний контур (після гідравлічного змішувача):
Т подачі = 67 °С; Т звороту = 55 °С.
У кількісних показниках пристрій рекуперації теплової енергії дозволив Замовнику знизити використання існуючих газових руфтопів до мінімуму із споживанням природного газу в середньому 250 м3/добу, що більш ніж у 3 рази нижче, ніж до реалізації проекту.
Впровадження проекту з рекуперації теплової енергії з компресорного обладнання «під ключ» включає:
- Розробку проектної документації;
- Підбір та постачання обладнання;
- Виконання будівельно-монтажних робіт;
- Виконання пуско-налагоджувальних робіт.
Керівник проекту: Денис Поліщук.
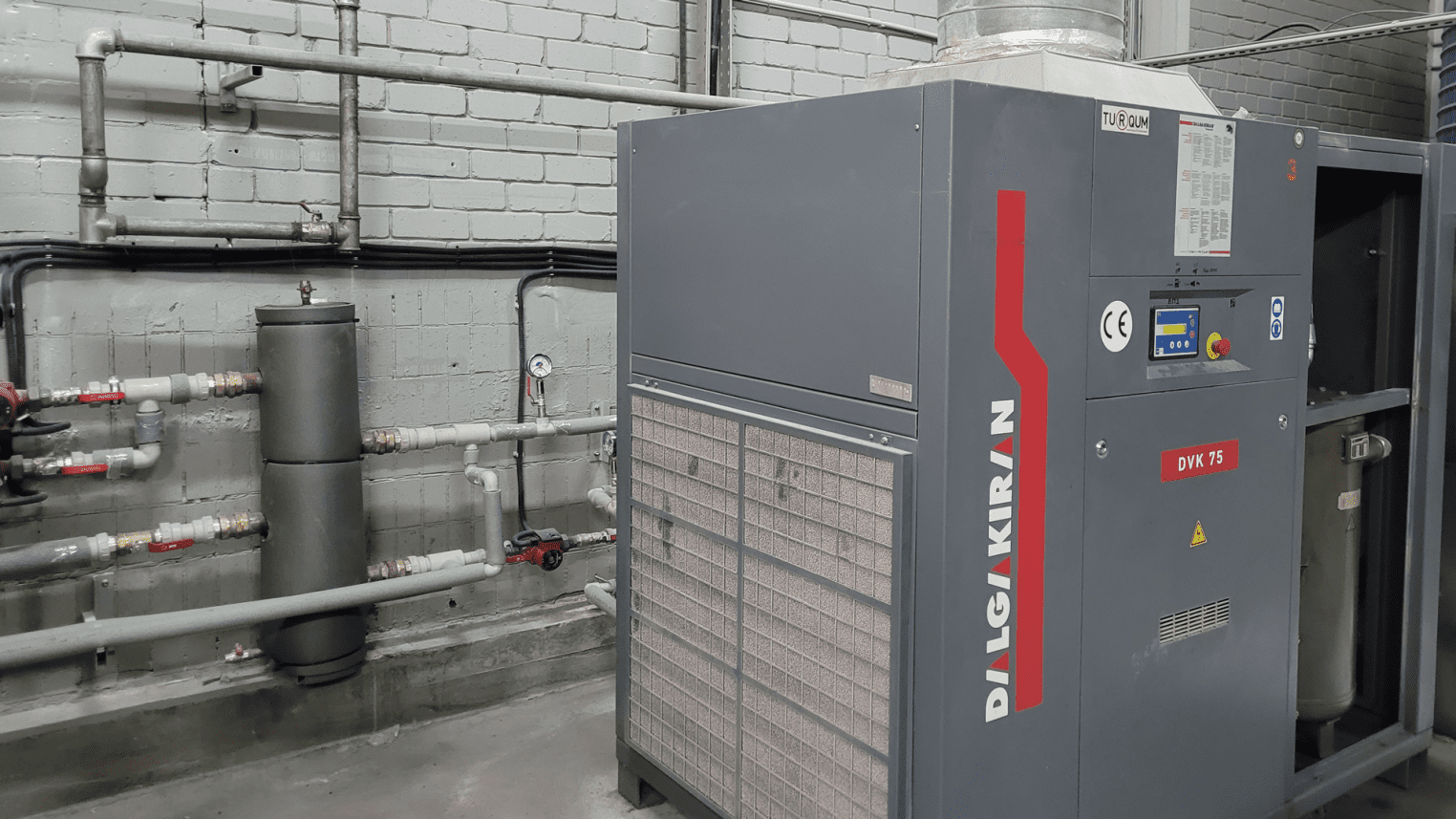
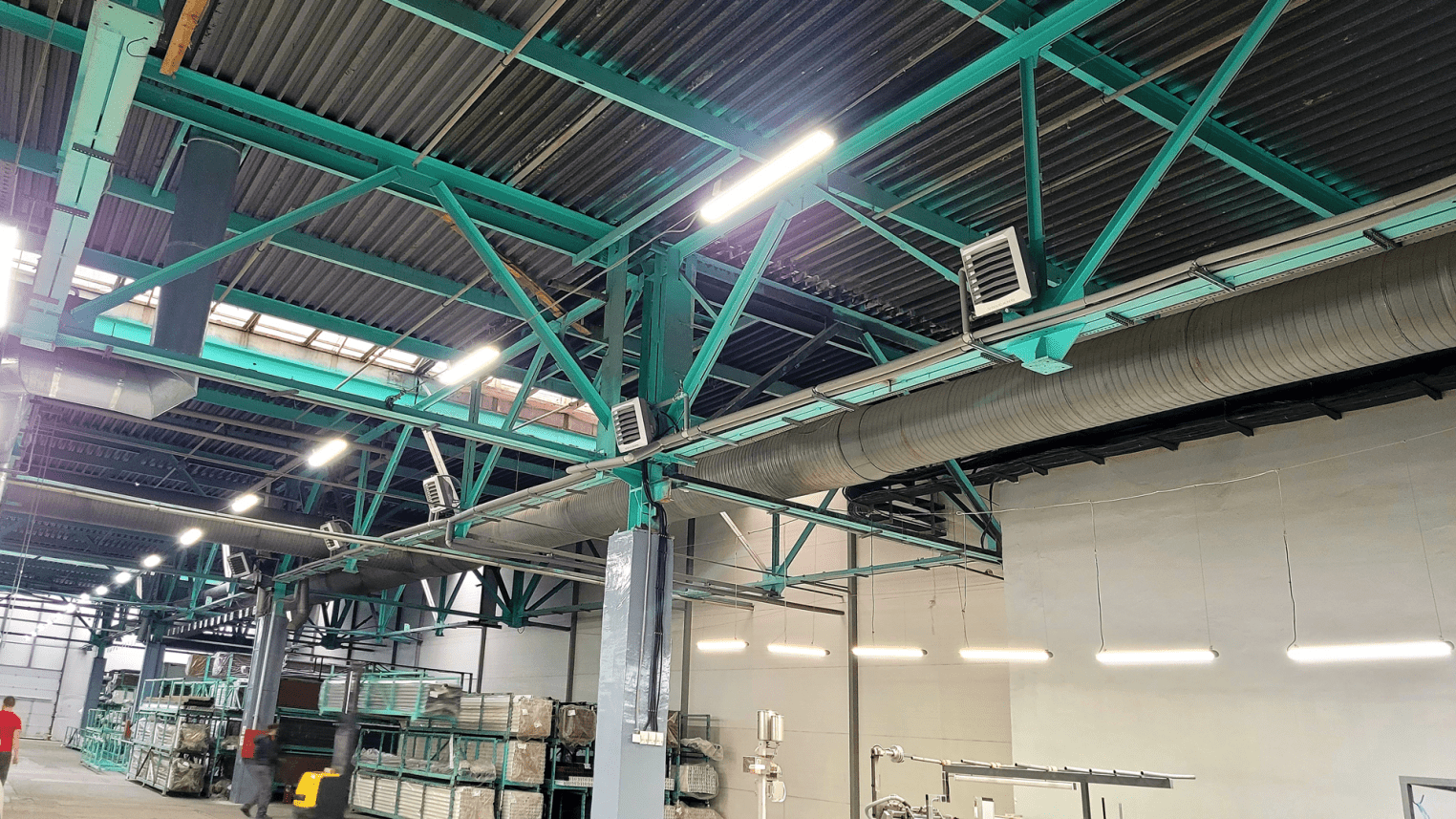
Залишити відповідь